Fire retardant wood : the impregnation process
Passive fire protection, of which fireproofing is a part, is a tool for conquering the wood products market in the construction of ERP (Establishment Receiving the Public) and interior or exterior fittings. Woodenha Industries has more than 10 years of experience in the fireproofing of solid wood and materials based on natural fibers: many buildings have been built using Woodenha Industries services.
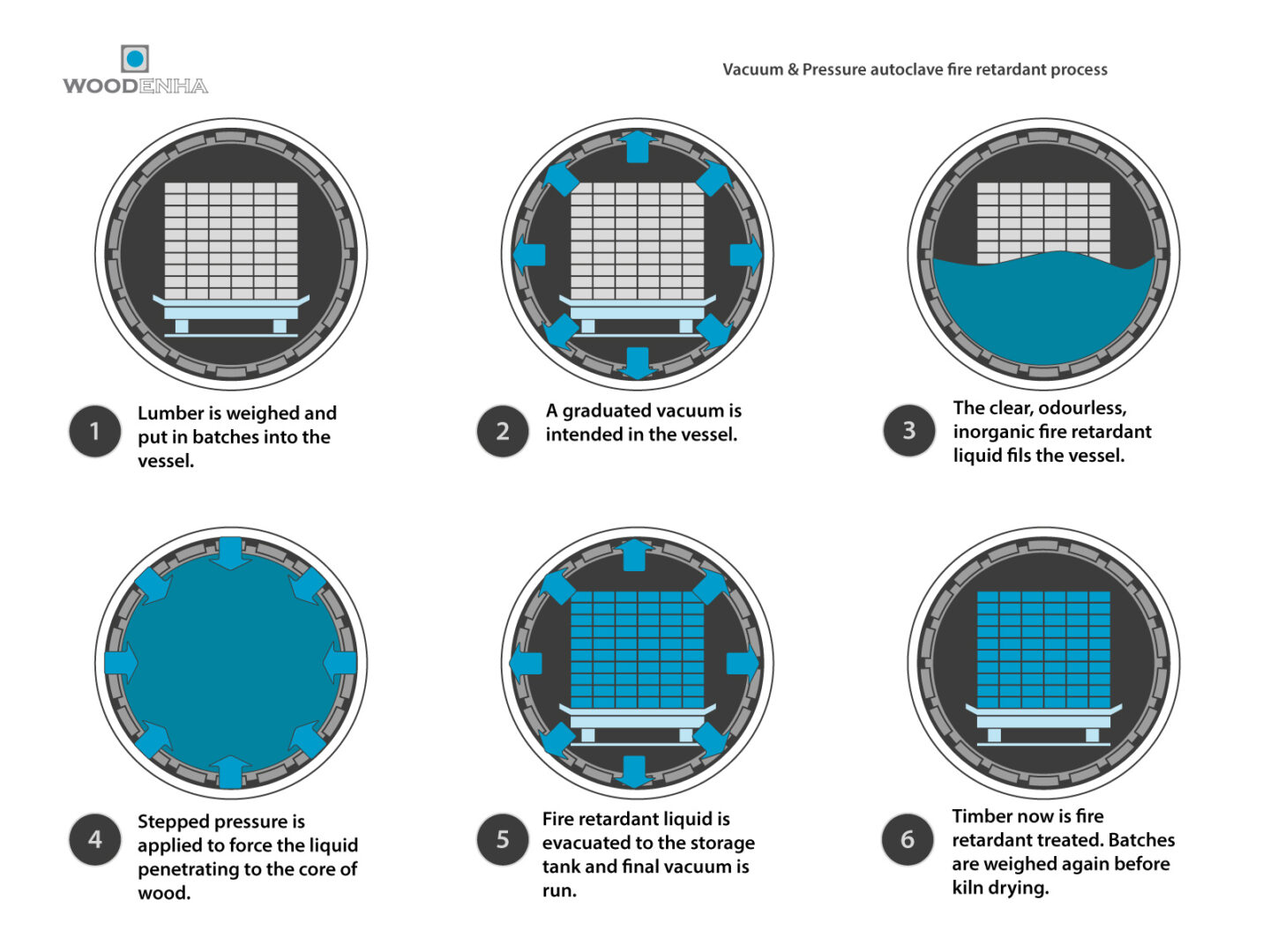
Impregnating the fire retardant liquid
Fireproofing is carried out in a specially designed vacuum & pressure autoclave in order to impregnate the fire retardant liquid right down to the core of the wood. Lumbers are first packaged in a specific and suitable way (1), then impregnated in the autoclave and finally dried (again) to the humidity suitable to the end use.
Within the autoclave device, Woodenha Industries injects a solution of water and active salts under pressure into the wood (2 & 3), the effect of which is to minimize the reaction to fire in the wood : limit inflammation and the spread of flame. This operation can only be performed correctly on dry wood. In order to spread fire retardant products well and to control their effectiveness, Woodenha Industries has developed a cutting-edge technique for wood conditioning and control of the impregnation process. The flame retardant is colorless, odorless.
The impregnation of the flame retardant liquid now happens deep in the material (4, 5 & 6). It is an efficient and sustainable process, thus giving the wood a very good reaction to fire; we speak of Euroclass B fire classification. Impregnation tends to slightly raise the wood fibers and may therefore require a posterior sanding in the case of interior use (decoration) or before the application of a finish – varnish, paint or wood saturator – which must be non-degrading.
Kiln drying
In order to stabilize the salts inside the wood and remove water from the solution, the wood must be dried to the humidity requested by the end use. This drying, the second in the life of the lumber in question, must be perfectly controlled to avoid on the one hand probable discoloration of the wood and on the other hand their deformation. It is necessary to refer to the DTUs (Official Technical Requirements) and standards in force to give us the targeted humidity which will be suitable for the use of wood in the building.
Flame retardant wood can at this stage receive a non-degrading finish such as varnish, paint or saturator.
A bunch of specific measures and batch traceability come along throughout the process : retention of fire retardant and wood moisture. The use, assembly, type of product, thickness and species of wood are fundamental parameters which will guide the way the flame retardant process will be done.
Looking for a fire expertise ?
Consult us for the opinion of a Woodenha expert